Mixer controls
PLC control systems:
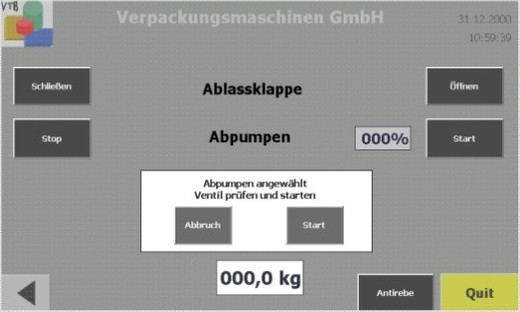
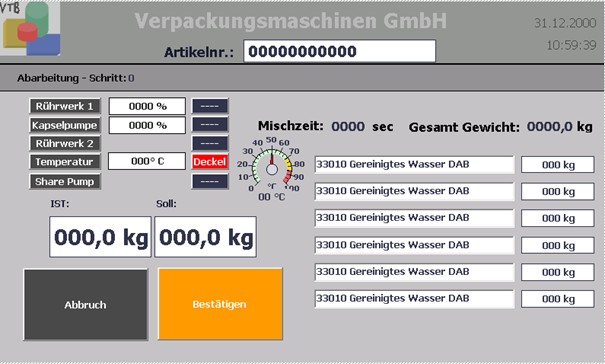
Our mixer control systems starts from simple time relays to high complex PLC control systems with connection to ERP – systems.
Specific characteristic of our software
- Mixer stage processing
- Temperature control (heating/cooling)
- Net weighing (mixer assembled on load cells)
- HACCP – process
- Control of external valves and feeding units
- User administration 21 CFR part 11
Print
Email
Kettle mixer
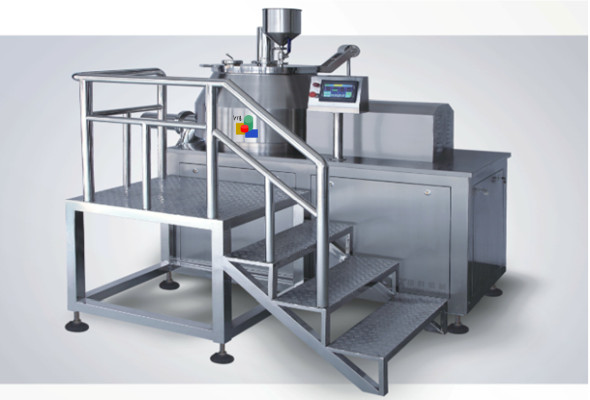
Material:
- Mixer barrel stainless steel 1.4301 optional 1.4571
- Base frame stainless steel 1.4301 optional 1.4571
- Cross-heading stainless steel 1.4301 optional 1.4571
Processing:
- The mixer tray is inside with 400th grain smoothed
- The outside surface is blank or optional with glas fragment blasted
- Massive load carrying system
Drive shaft support:
- Flange bearing with grease fitting
- Stainless steel roller bearing, twice sealed
- The seal is a compressing packing and a shaft seal with air purge seal
- Bearing: adjustment by the counter bearing, bridge bearing adjustable
Overall size:
- Standard 100 l – 1000 l
- (100 – 200 – 300 – 400 – 600 – 1000 ...)
Drive:
- Standard varnished
- Motors from 19 kW – 60 kW
Options:
- Easy mixer control unit, comfort mixer control unit or control unit with PLC for mixing program, mean control inside stainless steel cabinet
- Frequency converter for adjustment of speed
WORKING PRINCIPLE:
The process consists of mixing and granulating.
Powder metrical can be charged into the material pan from the conical hopper and continue to rotate in the container under the action of mixing blade once the hoper is closed. In the meanwhile, all materials grow up the shape of liquid bridge under continuous effects of conical wall. Under the action of extrusion, friction as well as crumb by blade and conical tank wall, all material is gradually turn for loosen. At last , while opening the hoper outlet, waterish particles are pushed off under the centrifugal effects of blade.
These soft particles are formed not dependent on forced extrusion effects, more exactly; mainly these small and uniform particles are formed after continuous cutting under the simile-liquid state. in all, this machine can realize the mutual transformation between different materials.
CHARACTERS:
- With consistent programmed technology ( man-machine interface if option selected ) , the machine can get assured of stability in quality, as well as easy manual operation for convenience of technological parameter and flow progress.
- Adopt frequency speed adjustment to control the stirring blade and cutter, easy to control the size of particle.
- With the rotating shaft hermetically filled with air, it can prevent all dust from compact.
- With a structure of conical hopper tank, all material can be in uniform rotation. The tank is laid with an interlayer on the bottom, in which water cooling circulation system featuring higher thermostatic performance than air cooling system is furnished, which leads to improve the quality of particles.
- With automatic lifting of the pan cover, the tank outlet matching with drying device, self-equipped arm-ladder, it is easy to operate.
- Lifting system with paddle is more beneficial to clean paddles and pot body.
- Mouth of material outlet has changed Into arc-shaped, avoiding up dead spaces.
Print
Email